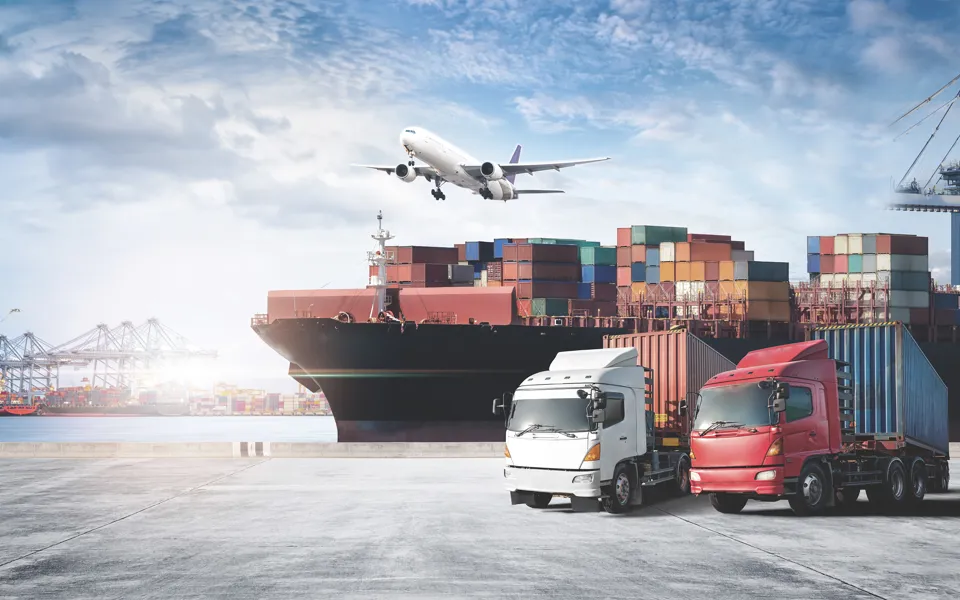
Richard Gordon, Project Director and Technical Authority for Fuel Cells at Ricardo. He comments on how fuel cell technology is supporting decarbonisation in a range of future mobility applications.
Fuel cell technology has a variety of benefits, but it’s application in maritime, commercial, off-highway and heavy-duty vehicles has the potential to deliver greater opportunities for OEMs.
When comparing fuel cell technology with pure battery electric systems it mainly boils down to the energy density of the complete system. In vehicles where the mass and volume of what is being transported is critical, then the fairly large mass and volume of a battery solution becomes a distinct disadvantage. A high-pressure gas storage and fuel cell system for a truck application, for example, typically has significantly less mass and occupies less volume than a battery solution, leaving more payload capacity. This is vital for this application, where less weight and more payload convert to more time on the road and increased profits for the operator.
Fuel cell technology is being actively developed for the marine sector, where a large amount of energy is required and where liquid hydrogen storage and fuel cell operations provides a solution where battery operation cannot.
Ricardo is applying its world-leading expertise across the full hydrogen value chain, including the design and development of hydrogen fuel cell propulsion technologies to power the next generation of zero emissions passenger cruise ships. The business is working as part of the sHYpS consortium, involving 13 partners in six European countries to accelerate the adoption of hydrogen as a renewable fuel in the maritime industry. The work has been funded by UK Research and Innovation (UKRI) under the UK Government’s Horizon Europe funding guarantee.
Ricardo’s role in the project is to lead the specification, design, build and test of a 375kW net usable power output fuel cell module and the design of a 40-foot containerised multi-MW power plant that combines the outputs of eight fuel cell modules. The containerised solution is intended to be installed within passenger ships. The project exemplifies Ricardo’s expertise in developing bespoke, optimised, high power, multi-stack fuel cell systems that deliver significantly enhanced power density by volume and mass. It also provides an opportunity to improve system efficiency and reduce system complexity and cost through increased integration and reduced component count.
As the pressure on the shipping industry to find solutions to achieve zero-emissions navigation in line with future global regulatory targets increases, this project is at the forefront of innovation to provide a very attractive proposition. Using hydrogen fuel cell technology to support the industry meet its sustainability objectives is now in a clear journey to deployability.
In addition to the application of fuel cell technology in the marine industry, we’re seeing interest amongst businesses within rail, the mining sector, off-highway machines, airport systems and stand-by generators, all of which see the benefits of the technology, and can also support it with refuelling requirements locally, at a hydrogen hub.
Sustainable mobility will be realised through the development of a range of technologies, working together to produce a variety of solutions for different applications. For example, green hydrogen and renewable electricity will exist side by side to fulfil specific needs, and fossil fuelled vehicles will be in use for a considerable length of time as renewables develop. These technologies do not stand alone, they require input and integration alongside other technologies. Therefore, an analysis of the whole fuel portfolio is necessary to truly understand the best solution by application.
Fuel cell technology is in its infancy when compared to traditional internal combustion technologies. Fuel cell and multi-stack systems are highly complex collection of sub-systems, typically supported by an electric air compressor, an electric hydrogen anode blower or hydrogen powered ejector, complex valves and sensors, humidifiers, water separators, physical structures that seal and hold it all together, the fuel cell control system and various safety systems. Taking the time to develop and optimise this technology is critical – and the challenge of supply chain, offering power range, robustness and low-cost options is all too real.
The fuel cell stack is the subject of intense development from the supporting materials and structures to the electrochemistry and catalyst materials to the optimisation of manufacturing techniques. This is focused on improving life expectancy, improving power density, reducing costs and improving overall system efficiency, such as PEM stacks operating at higher temperatures.
Fuel cell early adopters in the higher energy applications, typically operate out of a hub, port or depot and so providing hydrogen to that hub is not so difficult via tankers and stationary storage systems. These specialist applications have little holding them back to get started and are probably the most promising longer-term applications.
Reducing the implementation costs of fuel cell can be helped by standardisation of interfaces and materials, testing and validation approaches, growing supply chain availability and sharing of fuel cell systems across multiple applications and platforms. Anything that increases the manufacturing volume and eases the platform integration tasks.
Innovation in simplification is important. The fuel cell operation is highly complex, requiring the orchestration of a lot of interacting fluid flows perfectly to ensure stack life and performance. One example is the use of external humidifiers to maintain the ion conductivity of the fuel cell membrane. These are bulky devices which can be difficult to package.
Further innovations to increase PEM fuel cell operating temperature are also very important, as ~50% of the FC generated energy is lost to the coolant. The radiators of fuel cell vehicles tend to be very large to dissipate heat over a wide range of ambient temperatures. If the FC can operate at higher temperatures (over 90degC) then the radiator surface area can be reduced given “normal” ambient temperatures, significantly easing the integration challenge.
Other areas of supply chain focus include improving the capacity and efficiency of the electric air compressors required to boost air into the fuel cell along with potential energy recovery from the exhaust gas flow. These are fairly bulky and heavy and often required in duplicate at higher module power levels so difficult to package. Improvements here are very welcome.
So, for the larger vehicles with high specific power and energy requirement, hydrogen fuel cells make a lot of sense. For the smaller, lighter vehicles with shorter range needs, the battery electric approach shows many advantages. Both solutions have a very strong place in our journey to decarbonisation and both of which are developing fast.