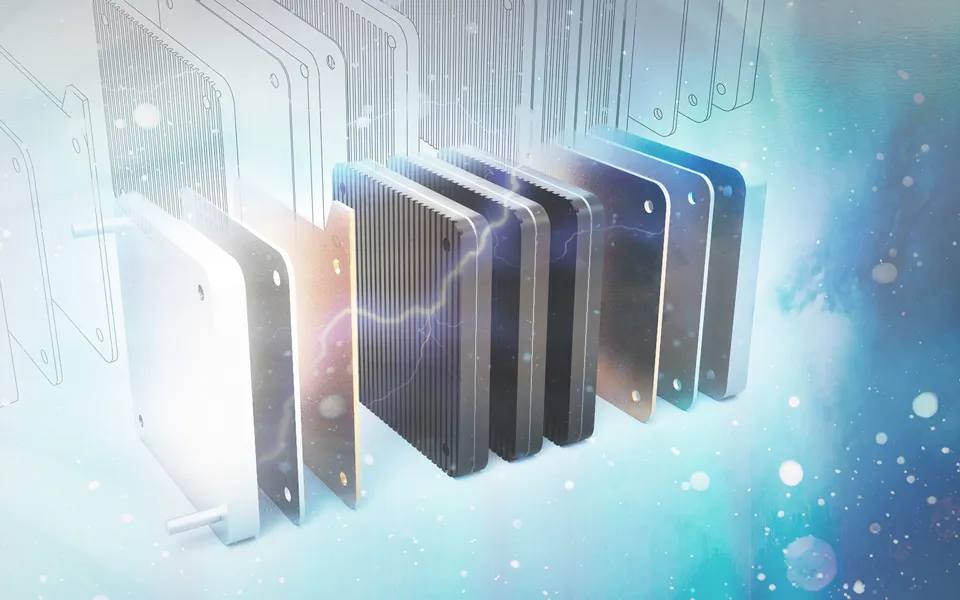
Hydrogen - the fuel fit for future mobility
01 Sep 2023
Hydrogen is increasingly becoming an important fuel source. Since 2019, governments worldwide have been releasing strategies that propose a reality where hydrogen could offer a means to cover a percentage of global energy use in the near future.
In the UK, hydrogen strategy and adoption featured heavily in the 2020 Ten Point Plan for a Green Industrial Revolution, with an ambition for 5GW of low carbon hydrogen production capacity by 2030 for use across the economy. The same year, the US Department for Energy’s Office for Fossil Fuel released its Hydrogen Strategy – Enabling a Low Carbon Economy and other countries and territories, including Australia, Japan South Korea and Denmark among others all have hydrogen strategies.
However, there is still some uncertainty surrounding the feasibility of hydrogen propulsion, and certainly, its clean production and safe transportation comes with limitations, making it unsuitable for some mobility sectors. So where do the opportunities lie, particularly for liquid hydrogen?
Undoubtedly, future decarbonised mobility will feature multiple forms of power plant, from batteries to hydrogen fuels cells and sustainable fuels. There is no one size fits all, and the choice depends on the type of mobility, range and power requirements. Small vehicles, including micro-mobility, and vehicles for short distances will most likely exclusively feature batteries, whereas larger vehicles that require higher power and that undertake longer journeys are more likely to view hydrogen and/or sustainable fuels as a viable option. For the latter, using hydrogen as an energy source, will also result in a further choice between an internal combustion engine to covert chemical energy into mechanical energy, or fuel cells to covert chemical energy to electrical energy.
Hydrogen fuel cells are being used as the favoured option in many mobility platforms due to their higher overall efficiency and cleaner exhaust gases compared to hydrogen combustion engines – and to minimise the size of hydrogen tanks, the gas can be liquified and pressurised. This process results in the hydrogen being cryogenically cooled to 20 Kelvin, or -250 Celsius. As this cold temperature sink is available in the vehicle, a synergy can be found between the electric powertrain that requires cooling and the hydrogen that needs boiling off before feeding it to fuel cell stacks. Combining these two needs, creates an optimised system that reduces mass and packaging, while also increases the overall system efficiency.
Inverter technology
At Ricardo we have taken steps to explore the feasibility of using liquid hydrogen to cool an electric powertrain. Handling of liquid hydrogen is extremely difficult, as the temperature gradient with respect to the surrounding environment is very large. In addition, hydrogen molecules are so small that they permeate through solids, creating failure modes not normally encountered in powertrains.
And finally, we need to understand if there is enough heat rejected in the powertrain to boil off and sufficiently warm up the hydrogen before it is fed into the fuel cell stacks, otherwise the stacks could suffer mechanical failure due to freezing moisture.
Our initial research focussed on these areas. Firstly, we modelled the heat rejection into the liquid hydrogen using computer fluid dynamics, where we modelled the fluid in two phases. When the hydrogen enters the propulsion inverter it is 100% in liquid form. When it exits, the inverter has partially turned the liquid to gas, which is then fed into the electric machine. As the fluid circulates around the cooling jacket of the machine it evaporates, expands and warms. Across the two components we have demonstrated that we can reject the power losses successfully and heat up the hydrogen from 20 Kelvin to 253 Kelvin (from -250 degrees Celsius to -20 degrees Celsius). The cooling circuits for the hydrogen are fully sealed and designed for high pressurised levels. In addition, they are made from metal alloys that are compatible with the use of hydrogen and minimise permeation. In the case of the inverter, we have partially thermal-isolated the cold plate and power modules from the enclosure to minimise heat leakage paths. In the case of the machine, the cooling jacket leaks heat to help with warming up the hydrogen to a temperature suitable for the fuel cells.
Where GaN plays a part
We have also been investigating the use of Gallium Nitride (GaN) semiconductor technology for propulsion inverters and learned and recognised that unlike silicon carbide semiconductors, GaN can operate at cryogenic temperatures with greater efficiency than at room or higher temperatures.
This work on GaN-based propulsion inverters was funded by Nexperia and following on from this, we decided to fund further academic research at Oxford University to fully understand cryogenic operation of GaN devices. This has paid off, developing our expertise on cryogenic performance that we can now exploit. In parallel, we have been developing hydrogen fuel cell technologies for land vehicles, aerospace and marine for several customer, as it has been recognised across all these sectors that liquid hydrogen has the potential to offer a fully maximised on-board energy payload. Since then, it’s been relatively simple to join the dots and appreciate the synergy between these two seemingly disparate topics. Ricardo has also funded internal R&D to look into the feasibility of such systems and we are now nearing the end of this phase. For our next phase, we aim to identify possible government funding routes and industrial partners to develop the technology to the proof-of-concept level, through a consortium led approach.
The benefits of liquid hydrogen
Simply put this boils down to how much energy a vehicle can carry and needs in order to fulfil its journey or maximise its range. Hydrogen fuel cell vehicles in operation today, not for research purposes, use compressed gaseous hydrogen tanks pressurised to 350 bar up to 700 bar. At 500 bar the energy density of hydrogen is 1.1kWh/L. By comparison, liquid hydrogen pressurised to only 5 bar has an energy density of 2.3kWh/L. For the same size tank and ignoring insulation requirements, liquid hydrogen has slightly more than twice the energy content, which translates to twice the range for the vehicle.
This opens the possibility of new operational missions, for example, as aircraft that could currently fly from London to Paris with gaseous hydrogen could reach Berlin, Vienna, and Milan if it were using liquid hydrogen.
Pushing technology boundaries
It is not however, that simple. Pushing technology boundaries is never straightforward and it not often achieved by a single individual or entity. There are a handful of research groups and commercial organisations exploring this space, and as with all research, baby steps are needed to build a foundation before moving on to an engineered solution. The challenges that we need to overcome relate to the handling of a large temperature differential between liquid hydrogen and the surrounding ambient and the handling of the liquid hydrogen itself.
Hydrogen channels needs to be fully sealed using compatible materials that minimise permeation and it’s vital that expansion and contraction of the hydrogen is managed, as it transitions from ambient temperature, for example 300 Kelvin (26 degrees Celsius) down to 20 Kelvin (minus 253 degrees Celsius). Material contraction is varies based on different points in the cooling channel, because hydrogen will be heated along the way, therefore the mechanical design needs to account for his variance in contraction.
Yet another challenge is that control electronics need to be maintained at a temperature greater than 220 Kelvin (minus 53 degrees Celsius). We can achieve this by housing the inverter in a partial vacuum and thermally isolating the cold plate and power module from the enclosure and from the control electronics.
A positive impact
Our focus is primarily on system optimisation of hydrogen fuel cell powered electric powertrains. The solution we are researching can be applied to road, aviation, rail and marine propulsion systems. Whilst we have concentrated on power levels of up to 250kW, in the first instance, the technology can be scaled up by modularising power units. We are currently investigating ways of using and scaling up GaN semiconductors for higher power levels. These devices currently only support low current capacities due to their geometry. To scale up power levels we have to parallel multiple devices, but this has its challenges because of the very fast switching speeds of this technology. Current sharing among devices during the switch transitions is not uniform due to mismatches in individual device parameters and parasitic elements and this could cause an individual device to overload and fail.
The benefits of R&D projects
Ricardo is an innovation powerhouse. We are constantly assessing the state-of-the-art technology and its limitations and talking to customers and industry bodies to understand needs and also technology and market roadmaps. Our R&D works across three-time horizons. A one-to-two-year horizon usually sees technologies ready for deployment. Many companies will be working across these technologies and competition is likely to be tough, however, a horizon of up to five years gives time and scope for generating IP and funding. Early adopters can have significant economic gains as they will have a monopoly for a short time. Our research on liquid hydrogen cooled powertrains falls into this horizon. There is also a longer-term vision, where we speculate on the different ways in which technology could evolve. This is more challenging for commercial businesses, as it is harder to quantify a return of investment made. However, working in partnership with universities and other organisations can make projects more financially feasible. The output allows us to create our own roadmaps and also guide our customers towards future mobility solutions.