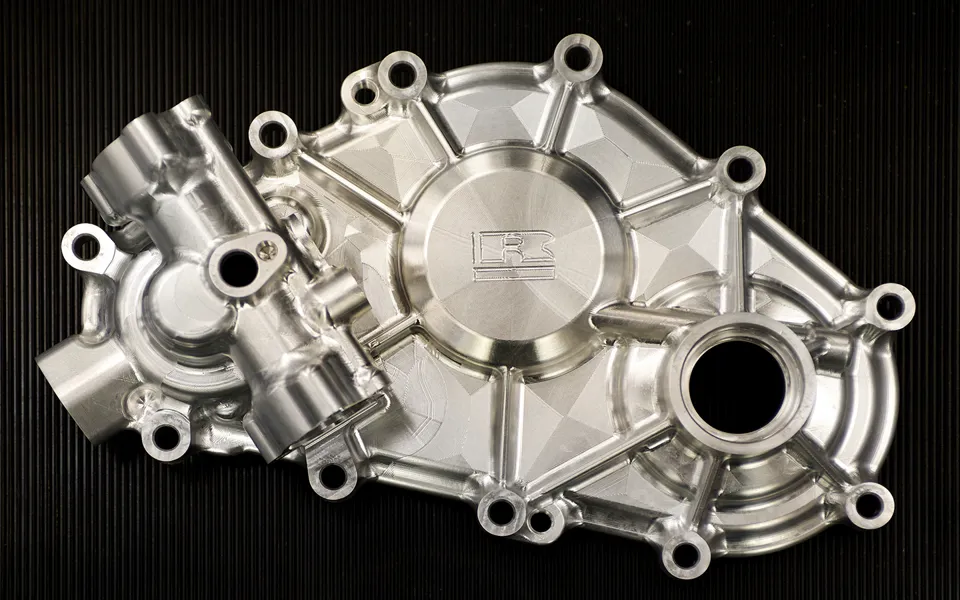
The future of motorsport transmissions
16 May 2024
A driver will shift gears around 3,500 times during a typical Formula 1 Grand Prix[1], and over 20,000 times in the 24 Hours of Le Mans[2]. These gear shifts need to be fast, seamless and efficient as over the course of a race, even a millisecond delay could add seconds of race time – which could be the difference between winning and losing.
The transmission is therefore a vital organ of any racecar, and over the last decade, has had to continually reinvent itself to keep pace with the evolving landscape of motorsport. The influx of hybrid and electric powertrains, along with regulations pushing the limits of reliability, has demanded new designs, development techniques and testing approaches. Looking ahead, the next ten years seem just as technologically turbulent.
The role of racing transmissions
A transmission, or gearbox, essentially converts the output torque from the engine or motor to the torque required to drive the wheels. This is achieved through gear ratios which allow the vehicle to accelerate, whilst also operating the engine or motor in its most effective rpm range.
In motorsport, the demands on a transmission are somewhat brutal. The fast speeds of racing mean the gearbox must endure high loads, whilst constantly delivering instantaneous and reliable gear shifts. It also needs to be lightweight and compactly packaged, yet robust enough to last several races, or in some cases, the entire season.
Speak to an expert about your transmission development requirements
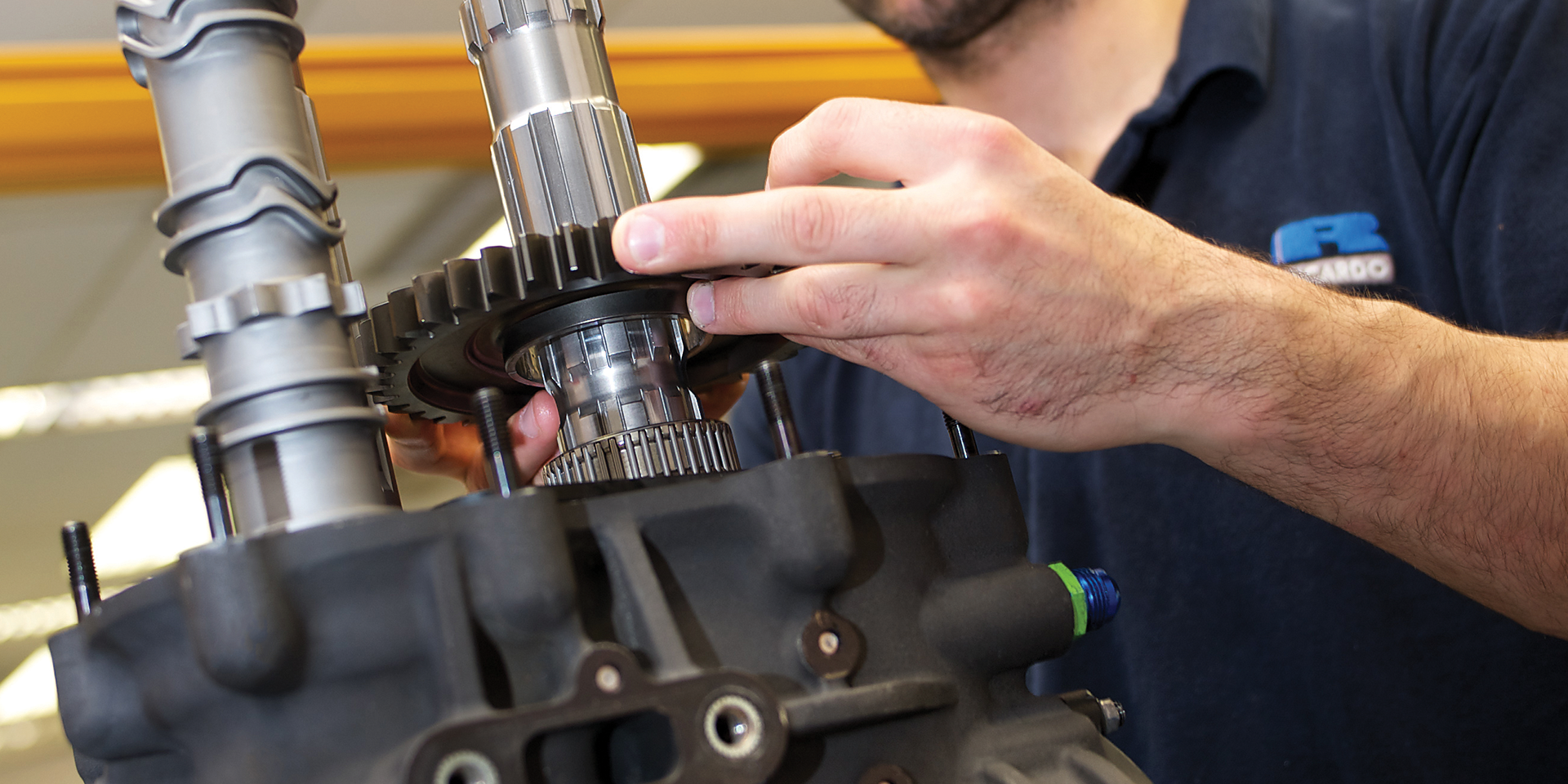
Transmission trends
There are currently three main configurations of powertrain racing today: Internal Combustion Engine (ICE), hybrid and fully electric. Each demands different characteristics from the gearbox to achieve optimum performance and this has led to the development of several different gearbox concepts.
‘Ultimately, whether it is an engine, hybrid or electric powertrain, you still need some type of mechanical output to deliver the right amount of torque to the wheels,’ highlights Stuart Cooper, Market Head for motorsport at Ricardo. ‘The gearbox layout for each powertrain type differs dramatically, but in essence, it still requires torque path components, whether that be a conventional ratio for an engine or a single speed gear for an EV. So, this array of powertrains now competing in motorsport just adds to our portfolio of transmission solutions.’
ICE vehicle transmissions
Racecars powered by combustion engines typically use sequential manual transmissions where drivers manually shift gears using either a shift lever or electronic paddles mounted behind the steering wheel. Each shift rotates a drum which has tracks on its surface. Selector forks follow the direction of these details which causes them to move either right or left and engage the dog clutch of the gear to the dog on an engagement ring, locking the gear to the shaft and allowing torque transmission.
Unlike the ‘H’ pattern of conventional manual transmissions, the sequential approach achieves faster and more reliable gearshifts. Furthermore, by having to shift in sequence, drivers cannot accidentally skip gears and select 2nd instead of 4th which could lead to an engine failure.
The most common layout for sequential manual transmissions in motorsport is Front Wheel Drive (FWD) where the engine, transmission and differential are located at the front axle. However, there are also some racecars that are Rear Wheel Drive (RWD) where the engine and transmission remain at the front, but drive is provided to the rear axle via a propshaft.
Hybrid vehicle transmissions
When you incorporate regenerative motors into the powertrain, the torque from the engine and the motors need to blend together to deliver the required torque at the wheels. ‘This means that the majority of transmissions used in hybrid vehicles are either automatic or DCT (Dual Clutch Transmissions),’ explains Steven Blevins, Head of Engineering at Ricardo. ‘In a similar way that the DCT actuates its clutches between pre-engaged gears, the hybrid drive element and ICE can be clutched in and out as required.’
EV transmissions
For fully electric vehicles, the motors provide consistent torque which is why many applications opt for a single speed gearbox. However, the most efficient, lightweight and compact approach is to use smaller motors with high power density that spin extremely fast, in some cases around 30,000 rpm.
However, the faster the speed of the motor, the less torque it produces. Consequently, for championships like Formula E, a single or double stage reduction is used to slow the driveshaft speed of the wheels to around 2,500 rpm and boost torque. This is typically achieved with a parallel axis arrangement where a single motor drives the rear wheels, and the torque is split via a differential.
An alternative approach is to have two motors back-to-back with an epicyclic reduction unit outboard on either side. This ‘sausage’ like arrangement allows the axis of the motors to be in line with the rear wheel axle and consequently directly feed the driveshaft.
‘Looking at the future regulations of all the championships, we expect three primary transmission concepts going forward,’ highlights Blevins. ‘The traditional sequential manual gearboxes for combustion cars, the parallel axis reduction ratio arrangement that you typically see in electric series such as Formula E and then this ‘sausage’ layout where an epicyclic feeds each individual wheel. Each will have a variety of combinations depending on whether they are located in the front or rear of the vehicle, but they will predominantly follow the same sort of concept.’
Learn more: our electric vehicle transmission range
The drive for efficiency
Accompanying the shift to hybrid and electric racing are regulations that push the boundaries of energy efficiency and reliability. Teams are limited by the amount of fuel that can flow into the engine and the amount of power they can deploy through the batteries. Consequently, every joule of energy is precious and needs to be transmitted to the wheels in the most efficient way possible.
‘The requirements of a gearbox are generally similar for any series and that is to minimise losses,’ says Blevins. ‘Losses mean you are losing energy through heat, vibration and noise, which could otherwise be converted to traction at the wheels. Efficiency has always been a focus in transmission development but today it is more important than ever.’
However, it is no good having a highly efficient gearbox if it only lasts for half the race or is overengineered to last much longer than required. To strike the perfect balance between efficiency and life, in a lightweight, compact package, manufacturers are expanding their simulation and testing activities.
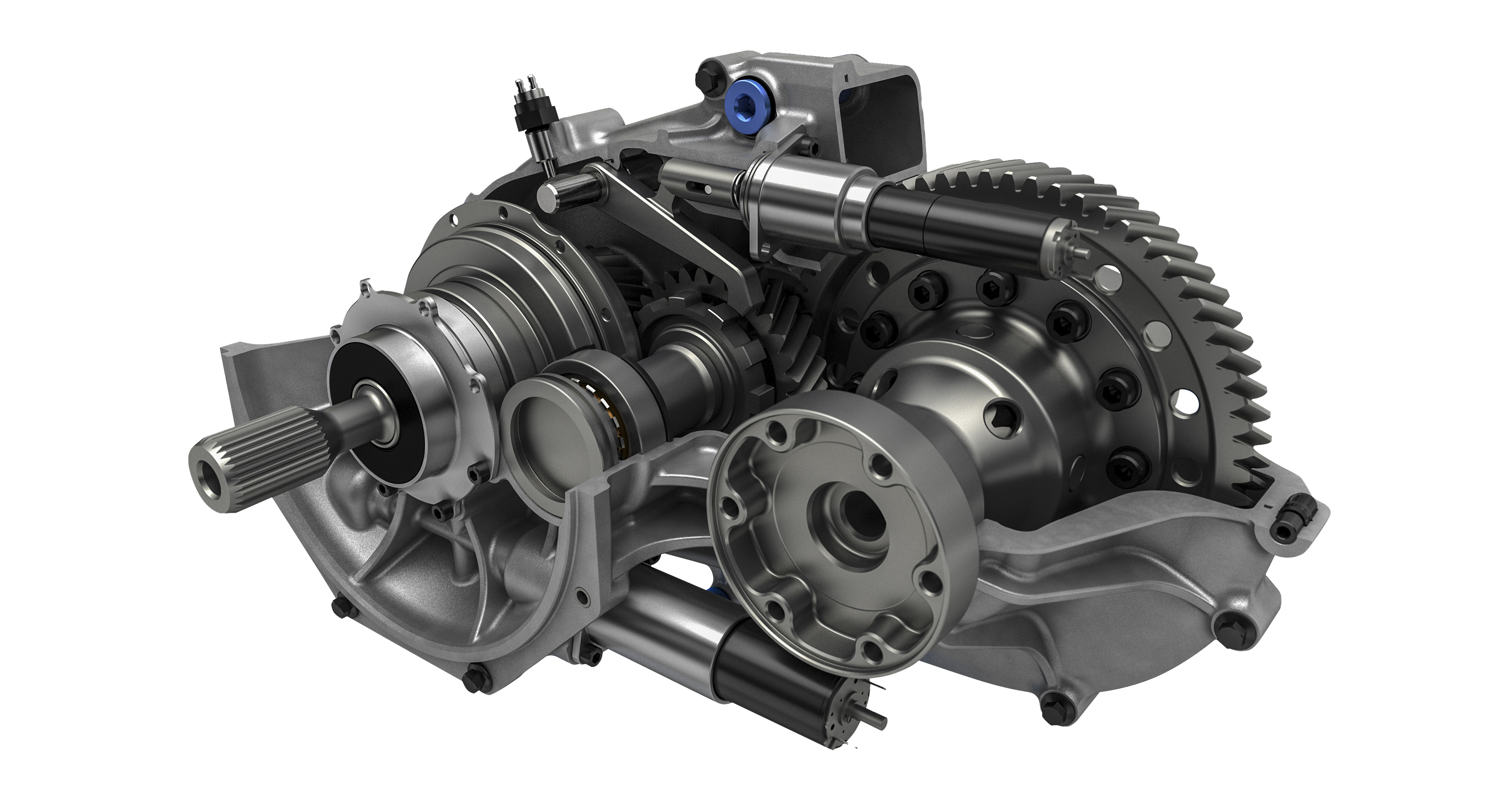
‘Unfortunately, there are only a few test rigs out there that are capable of testing these high speed motors,’ reveals Cooper. ‘Test rigs were originally designed to test combustion engines operating at around 8,000rpm, but with motors now exceeding 30,000rpm, this is much more of a challenge. There are very few facilities where you can run the entire drivetrain package, and those are often fully booked for automotive. So, at Ricardo we are looking for ways to adapt our existing facilities to provide flexible configurations for testing a wide range of speed and torque inputs. On occasions this means gearing up the input speed of the rig input motor to achieve the high input speeds that many EV gearboxes require.’
Read more: Motorsport trends, opportunities and challenges to look out for
Standardisation
Another trend has been the rise of standardisation. To keep costs down and grids full, series are moving towards sole suppliers providing standardised parts rather than bespoke solutions. This adds to the challenge of developing transmissions because the same gearbox now has to suit a variety of different racecars and configurations.
‘Series operators are now more in control of the technical direction of the championship and rely on a few suppliers to deliver high performance and reliable components to the entire grid,’ highlights Blevins. ‘This approach not only saves money but also equalises the competitiveness of the cars which ultimately leads to more exciting racing.’
‘From a supplier point of view though, it requires established manufacturing capability, a reliable supply chain and techniques to equalise the performance of parts. We have extensive experience in this as we have supplied championships from Rally through to Formula E, helping them benefit from a cost effective yet high performance transmission package.’
Did you find this article useful? Book a consultation with Stuart or Steve about developing a bespoke transmission solution for your platform
References
[1] Explained: Driver Workload During a Lap[Online]. Mercedes AMG Petronas Formula 1 Team.
[2] 2021.Race of extremes: 28 million sparks and 20,000 gear changes[Online]. Porsche.
Subscribe or ask us a question
Subscribe for updates or get in touch with our experts about this article or about our motorsport services, or email us at info@ricardo.com