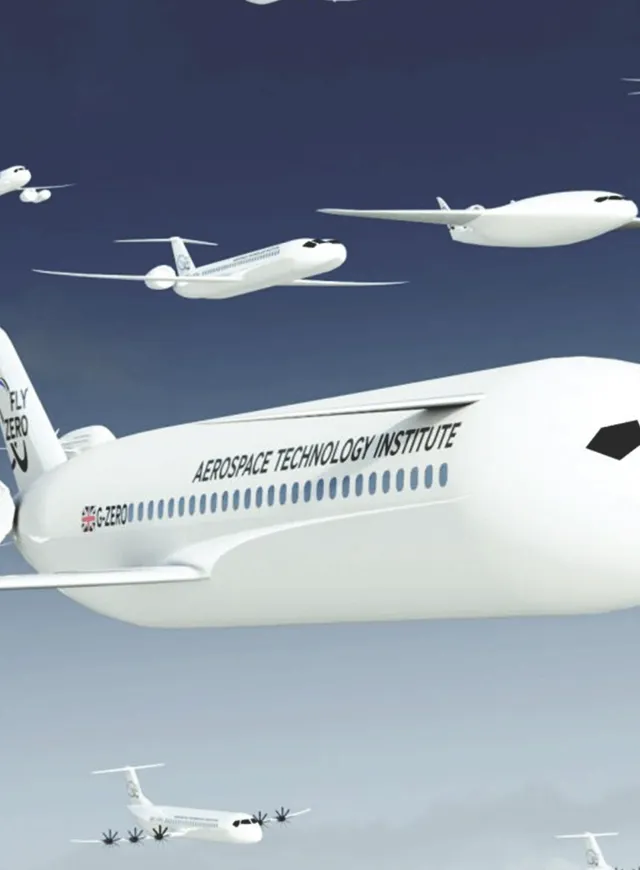
FlyZero: hydrogen ICE for aerospace
Applying its world-renowned expertise in hydrogen technology innovation and integration, Ricardo has helped the UK Government-backed project to take a significant step forward in its goal of realising zero carbon emission air travel.
Challenge
FlyZero is a one-of-a-kind research project aiming to realise zero carbon emission commercial aviation by the end of the decade. The intensive 12-month strategic research programme is bringing experts together from across the UK to conduct a detailed and holistic study of the design challenges, manufacturing demands, operational requirements and market opportunity of potential zero carbon emission aircraft concepts.
Together with the technology roadmaps, market and economic analysis, and lifecycle sustainability assessment, the findings from three concept aircraft will support the UK aerospace sector in standing at the forefront of sustainable flight in design, manufacture, technology and skills for years to come.
Approach
- By fusing propulsion, energy storage and airframe technologies to create ‘scout’ aircraft, the FlyZero team has assessed the capability of novel technologies investigating how propulsion systems applied to each scout aircraft meet requirements such as payload, range, speed, materials, economics, operations and non-CO2 emissions.
- For this study the target aircraft scouts are sub-regional, regional and single aisle passenger aircraft from 50 to 150 seats with a range from 500 to 1000 NM. This sector is currently serviced by gas turbine propulsion systems in jet and turboprop forms using fossil-based jet aviation fuel
- Propulsion system and energy storage options were assessed across realistic flight mission profiles (take-off, top-of-climb, cruise) appropriate for the scouts under consideration
- There are a wide range of zero carbon inflight options but all potential energy vectors and corresponding propulsion systems have differing challenges requiring multi-dimensional comparisons to evaluate trade-offs and technology gaps. Internal combustion engines supported by electrification and zero carbon-in-flight fuels such as hydrogen are a valid contender for evaluation
- The objective of this work package was to evaluate via a desktop study, the feasibility of internal combustion engine-based propulsion systems to meet the zero carbon in-flight mission targets for the FlyZero aircraft concepts
- The concept evaluation phase focused on rapid assessment of a longlist of candidate solutions. Recommendations were made for concepts to take forward for further evaluation
- The final phase - concept development - was to identify concepts in more detail and develop a technology roadmap to 2035 showing technology readiness levels for key sub– systems and technology gaps for focus within the wider FlyZero project aims
- For FlyZero, Ricardo assessed candidate propulsion system options based on scalable internal combustion engines using zero carbon fuels, including the potential benefits of electrification/hybridisation
- Candidate propulsion system architectures included conventional four-stroke vee-format, rotary/Wankel, two-stroke and opposed-piston two-stroke, driving a propeller, in an equivalent configuration to a turboprop baseline
Results
The project has identified a non-hybridised, spark-ignited, V12 engine module burning liquid hydrogen as having the highest potential to power the next generation of commercial aircraft owing to its very high power to weight ratio and zero carbon emission credentials.
In the first output document published, Primary Energy Source Comparison and Selection, FlyZero calculates renewable liquid hydrogen to have approximately three times the available energy content per kg of fuel carried on board an aircraft compared to kerosene, approximately six times that of ammonia and approximately sixty times that compared to a battery.
Recommendations
A hydrogen-fuelled, spark-ignited internal combustion engine is a credible concept for regional and sub-regional zero carbon flight especially in comparison to fuel cell and battery electric.
The study explored propulsion system architecture trade-offs and arrived at some useful conclusions:
- Aircraft-level propulsion plus fuel mass is minimised by a small number of larger
powerplants (eg two per aircraft) rather than a larger number of smaller powerplants. Fewer, larger powerplants will therefore allow maximum retention of existing aircraft attributes such as payload and range - A two-speed gearbox solution to allow internal combustion engine efficiency to be optimised between take-off and cruise further decreases fuel mass, again minimising payload/range impacts
- Any form of hybridisation (ie sizing the thermal powerplant for only part of the mission and supplanting with battery energy storage and an e-machine) only resulted in a significant increase in overall propulsion + energy system mass and volume; which would significantly harm payload and range
- One of the main selling points of the scalable hydrogen internal combustion engine concept is a relatively mature supply chain so it could be used as a bridging solution to hydrogen gas turbines (some years away) or as a way to get demonstrators in the air to accelerate interest and show feasibility of other hydrogen systems (eg fuel tank)
- Renewable liquid hydrogen has massive potential in terms of energy density as a primary fuel source for commercial aviation
- This reconfirms real value in overcoming the challenges around storing and utilising cryogenic hydrogen on board an aircraft which also presents an opportunity for the UK aerospace sector to secure a share of this market
- FlyZero is also investigating the production and distribution of hydrogen at scale which would be required to replace conventional aviation fuel at airports in the UK and overseas with findings set to be included in the end of project reports