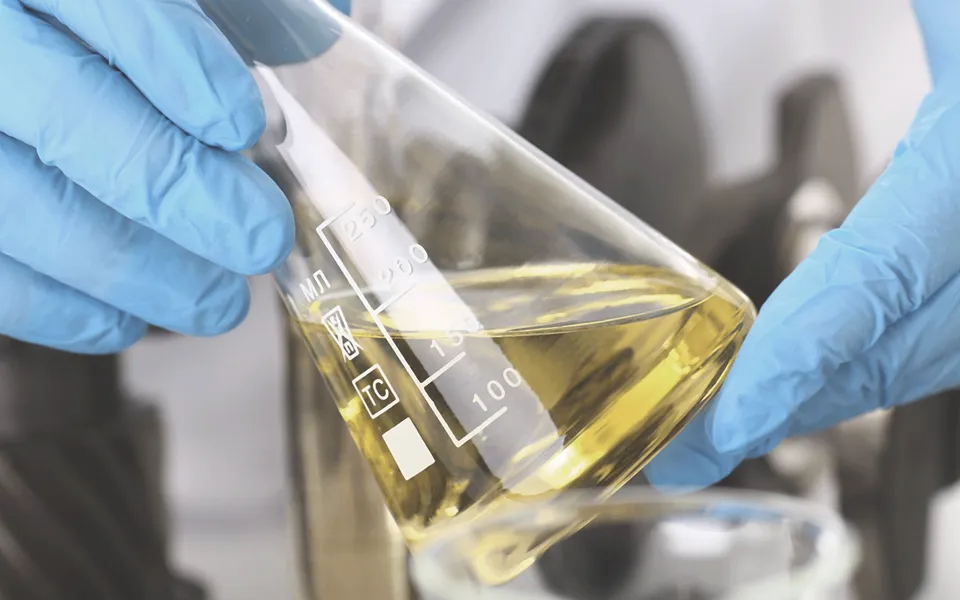
Is there a future for fuels on the road to 2035?
15 Jul 2022
There’s little doubt that battery electrification is one of the most efficient ways to store and convert energy with low losses. However, for heavy duty applications there is likely to still be a place for the internal combustion engine in the product mix of the future, even beyond 2050.
European legislation is pushing towards a 30% fuel consumption reduction by 2030 on heavy duty applications (37.5% for light duty), although these figures are likely to increase as the Fit for 55 legislation is developed. This is driving further technology advancement and economic benefits to customers, and as a result local policymakers could mandate an increased penetration of lower carbon fossil fuels.
Carbon reduction needs to continue towards 2050 and there are questions that remain unanswered, such as can electric vehicles meet the needs of all heavy-duty segments, and is it the right thing from an LCA point of view? Fuel cell maturity and durability are also key factors for applications in heavy duty products.
Combustion engines can serve many requirements by running on zero carbon or carbon-neutral fuels – they are relatively cheap, capable, and robust in extreme conditions, with high durability. There is also existing widespread global production and supply base both for engines and for the distribution of their fuels. There are three broad types of renewable fuels that serve low carbon requirements, and well-defined pathways exist.
Biomass-based fuels
The first two groups are biomass-based fuels. First-generation biomass is crop-based, made from for example rapeseed and sunflower oil. Second generation biofuels are made from biomass like forestry residue, and waste substances like waste cooking oil and farm slurry. Biofuels use biomass, electricity (ideally renewable), and broadly mechanical or organic chemistry processes.
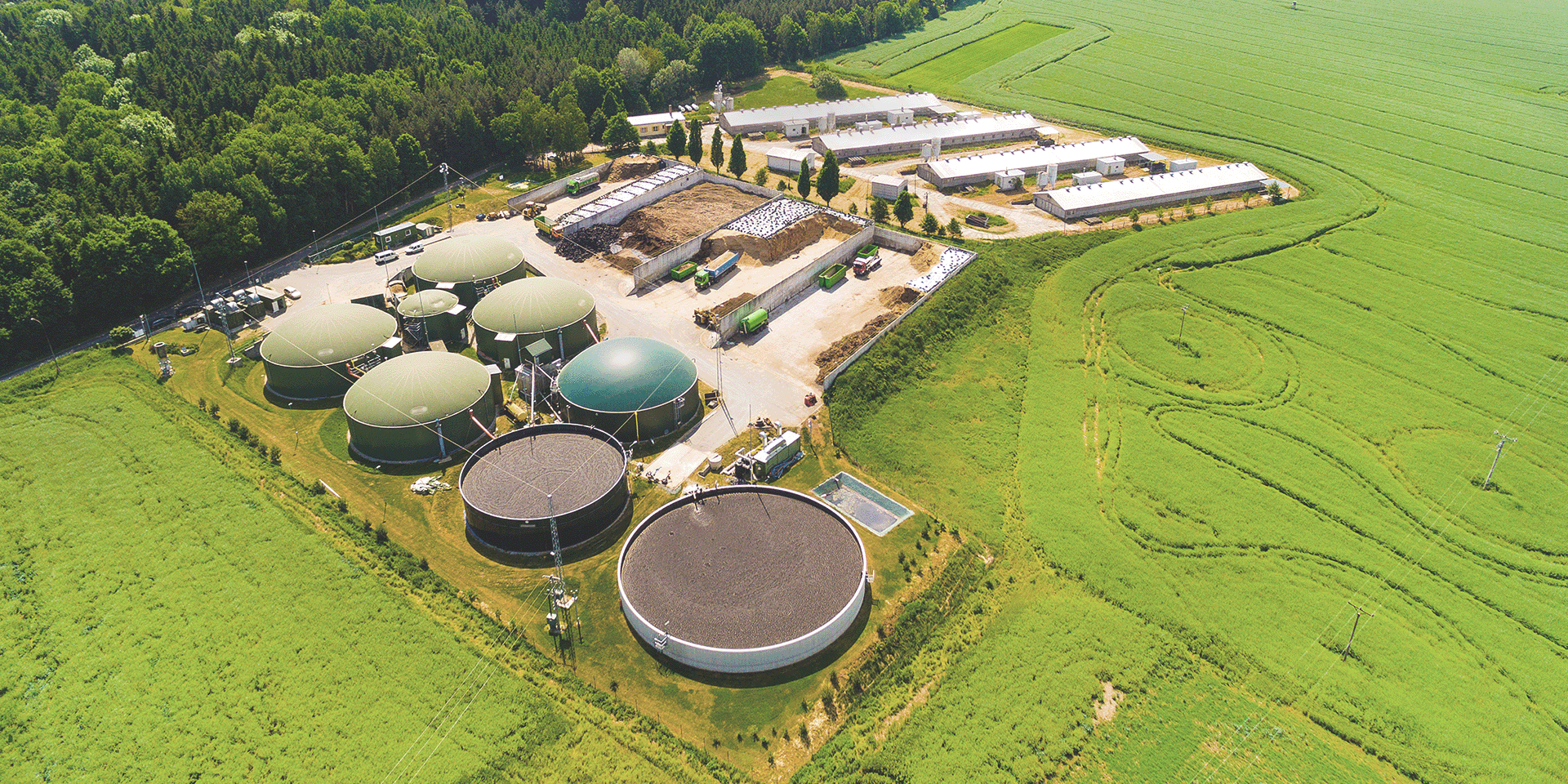
Synthetic biofuels involve gasification or steam reforming of the biomass to create a synthesis gas consisting of hydrogen, carbon monoxide and carbon dioxide that can be further processed to create combustion fuels.
Despite their potential to make rapid improvements to net carbon emissions, first-generation biofuels have had several challenges, including food and fuel competition, land use, impact on the natural carbon sink, and carbon dioxide and nitrous oxide emissions associated with agriculture. Second generation biofuels have challenges associated with the control of biomass harvests to sustainable levels, land use change and production scalability.
E-Fuels
The third group – electro-fuels or e-fuels - don’t involve biomass but use a waste carbon dioxide stream from an industrial process, a bioenergy plant flue, or direct capture of carbon from the air.
Zero carbon renewable fuels need to be carefully selected because they can be expensive to produce in terms of energy invested per unit of energy stored in the fuel. This critically depends on the elements of the fuel pathways and the energy mix involved in creating, storing, and transporting fuel.
Fossil fuels require little energy to extract and refine compared to their stored energy, with relatively low greenhouse gas production in this phase. However, when they burn, new CO2is released and is added to the atmosphere. For electro and biofuels, combustion does not produce new CO2, so it is not treated as a net release. Biofuels have a wide range of energy cost and CO2 emissions; the least costly are those fuels from waste cooking oils and waste from paper production.
It’s no surprise that these fuels are amongst the most economic, but in some instances, they may become feedstock limited. E-fuel pathways are low carbon, but as previously mentioned can also be highly energy intensive. Generally, the simpler the molecule, the lower the energy cost.
Green hydrogen (or e-hydrogen) and e-methane are potentially seen as attractive options as long-term future fuels for road transport. The introduction of an e-fuels enables a pathway towards zero emissions for internal combustion engines, and this could be implemented as e-methane (or bio-methane) dilution of natural gas.
Most e-fuel options will require a spark-ignition combustion system. Ricardo envisages that OEMs will require sustainable heavy-duty engines in their powertrain portfolio. A heavy-duty spark ignition engine concept with a high commonality of base engine, and key systems modified to suit different fuels, according to market demands is expected.
Ricardo has already commenced the development of its hydrogen fuelled engine concepts, based around two possible configurations, minimum change from a diesel base engine, and an engine fully optimised for hydrogen fuel. An early analysis of total cost of ownership for various future truck options compared to diesel battery, electric, fuel cell electric and hydrogen fuelled internal combustion engine found that the hydrogen fuelled engine application is attractive compared to the electrified variants. Efficiency of traction for high-load application is relatively similar between the fuel cell and internal combustion engine powertrain. The vehicle fuel infrastructure is also similar between the two variants – although cost differentiators may impact decision making.
Fuel cell electric vehicles require fuel storage, fuel cell, power electronics, a traction motor, and battery. The simplest engine product needs just the fuel storage, engine, and transmission. This analysis lends weight to the argument that the internal combustion engine should feature in the future product mix.
A blog by Trevor Downes, Chief Engineer - Engines and Emissions Control