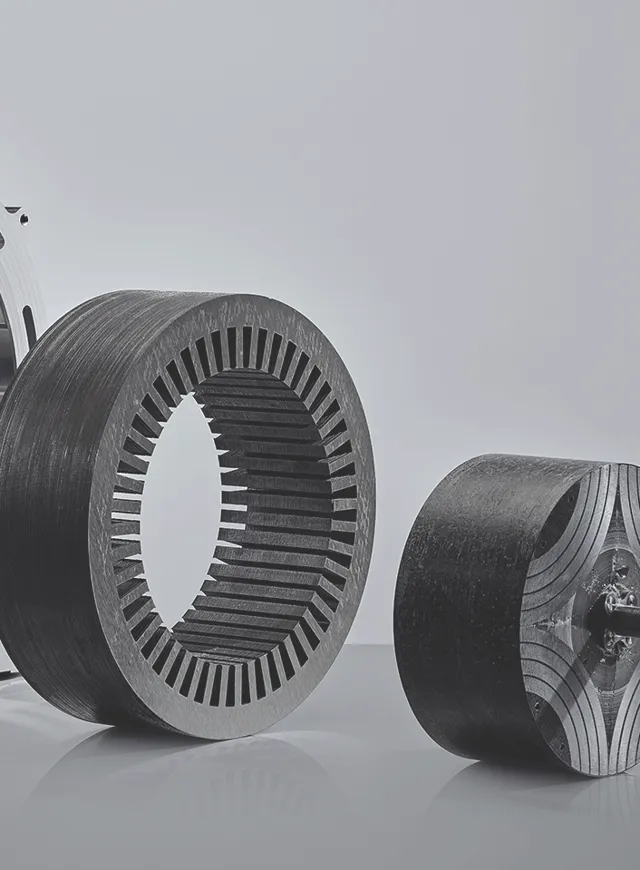
Sustainable electric motor supply chain
Download nowCase study - Sustainable UK electric motor supply chain
Leveraging national supply chains and engineering expertise to create the technology needed to
kickstart the UK’s green industrial revolution and to meet net zero targets
The UK-ALUMOTOR consortium is building the UK’s electric motor supply chain by leveraging our manufacturing expertise to deliver the next generation of sustainable electric motors
Challenge
The UK government has committed to reaching net zero emissions by 2050. The transport sector accounts for 24% of all greenhouse gas emissions in the UK1, remaining the largest emitting sector despite the reduction in road transport usage during recent national lockdowns. For the UK to be able to meet its ambitious net zero emissions targets, there is a requirement to reduce the environmental impact of the transportation sector across the full vehicle life cycle.
Electrification is one route to the reduction of vehicle emissions on our roads. To support the effective mass adoption of electric vehicles, vehicle manufacturers need to make it an affordable option for the consumer whilst ensuring that design and manufacturing processes are commercially viable and environmentally sustainable.
The global market for electric motors is estimated to be worth £28.5 billion by 2025. It is essential that key players in the UK electric vehicles manufacturing sector, supported by government, act now to enable the nation to capture a significant slice of this substantial growth market.
Approach
The UK-ALUMOTOR consortium is led by Ricardo with Aspire Engineering, Brandauer, Warwick Manufacturing Group at The University of Warwick, Phoenix Scientific Industries, and Global Technologies Racing.
It was formed to develop the UK’s manufacturing capability around electric vehicle components, and a UK based supply chain around an innovative proprietary design for an electric motor for passenger car and light commercial vehicle. The consortium is also investigating higher performance derivatives, suitable for defence and motorsport applications.
UK-ALUMOTOR is a step towards developing the predictable supply chain and stability in pricing necessary to enable OEMs to deliver affordable electric vehicles which support the mass adoption of electrification. The programme is developing and refining a rare-earth magnet-free sustainable electric motor concept with aluminium stator windings, which retains the key attributes of magnet-rich motors. The design will be tailored for UK manufacture at volume production.
The goal is to create technology that is robust, costs less than current products and reduces lifecycle impact by eliminating the use of scarce resources. The aim is to remove up to 12kg of rare-earth magnets per machine, and to reduce the amount of high acidification materials such as copper without impacting motor function or quality. This approach dispenses with the need for costly materials, reduces the environmental impact of production, and disrupts existing supply chain monopolies.
The UK-ALUMOTOR consortium was recently awarded government funding from the UK Research and Innovation’s Driving Electric Revolution Challenge fund.
Results
- Supporting the UK’s net zero ambitions. UK ALUMOTOR will develop a more affordable, environmentally sustainable design which displaces the need for scarce material resources, resulting in a greener and more affordable solution to support the mass adoption of electrification.
- Boosting the UK economy. The development of a class-leading e-machine product and a UK supply chain for the manufacture of Power Electronics, Machines and Drives (PEMD) will allow the UK to capture a substantial growth market, programmed to be worth £28.5bn by 2025.
- Training the next generation. UK-ALUMOTOR will grow the UK’s PEMD manufacturing capability and train the next generation of skilled engineers and technicians, positioning the country at the forefront of the global electric revolution.