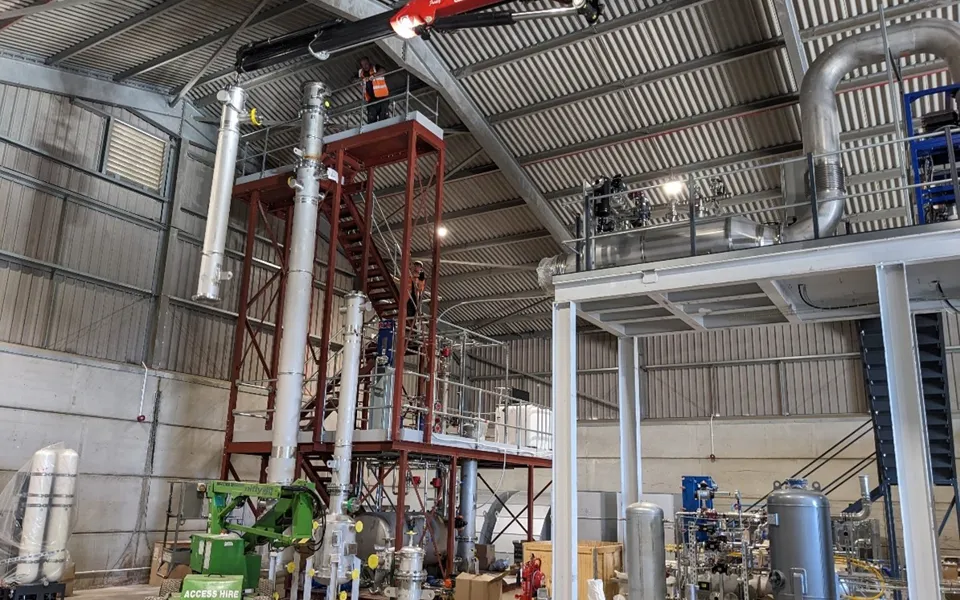
How automotive digital engineering techniques are improving efficiency and performance and reducing risk, cost and time to market for energy transition solutions
31 Jan 2024
Ricardo is designing, installing and operating a combined heat and power demonstrator plant with a carbon negative footprint to showcase climate repairing technology, and demonstrate the effectiveness of community scale negative emission technology plus clean energy using sustainably-sourced forestry waste. Here, Dr Gareth Milton, one of the lead engineers on the project, explains how using a model-based approach, which is a highly effective best practice in automotive engineering, is being applied to this new domain energy transition, to remove technology development time, speed up decision-making and enable a ‘right first time’ outcome.
A strong track record in simulation and control within automotive research and development
I started working at Ricardo in 2007 as part of the control and electronics team. I worked on a range of powertrain projects which included a lot of electrification and hybridisation, as well as applying advanced and optimal control techniques for clients. About a decade ago, I had the chance to lead the ADEPT project, for the UK Government’s Innovate UK, which focused on the mild hybridisation of diesel engines and featured an interesting concept of waste heat recovery. This led to me getting more involved in research and development (R&D) at Ricardo, and subsequently for a number of large-scale Ricardo automotive research projects funded either by the UK Government or the European Commission. On these, I was the technical lead for optimal control: in other words, maximising efficiency of the vehicle through advanced control.
I have brought my experience of simulation and control from automotive engineering to Ricardo’s latest project in community-scale negative emission technology and clean energy. I am looking at how we can apply our automotive engineering tools and techniques to the development of this novel technology so that we can get to our desired system much more quickly and efficiently than is possible through the traditional industrial process.
The benefits of applying automotive know-how to energy transition
In automotive, over many years of consulting for our clients who have very tight deadlines and margins for their product programmes, we have developed ever more sophisticated and effective virtual engineering techniques and practices, often having to work to very rapid technology development cycles and identifying ways of reducing the amount of time spent on physical testing, in order to validate designs earlier in the product development cycle. With over a century’s experience and expertise in successful innovation for the automotive industry, we know that these tried and tested tools and techniques can be applied to other industry sectors and domains which are perhaps only just now having to address technical challenges that have long been solved within our sector of engineering.
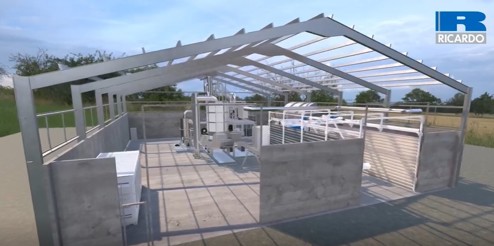
What we have done is to take a modelling and simulation-led approach to the design cycle for the demonstrator plant. While our 3D CAD team worked on the physical design for the plant, we applied a model based approach to the process and control design, whereby we were able to test out the concept virtually before we launched the procurement cycle for the plant. We also successfully used 3D real-time technologies, virtual reality and augmented reality to support the design and installation of the plant, notably to enable our engineers to stand virtually on the top platform close to the roof, assessing clearances, while physically being on the floor in their office. By applying this approach to the plant for end users in multiple industry sectors, including power generation, food and drink manufacturing, concrete production and agriculture, we are helping our clients achieve greener operations sooner.
How we optimised performance for the plant design
From the very beginning, our objective has been to make the design of the plant the very best that it can be against a set of requirements and attributes, even before any physical work begins on the project. We have applied a series of optimisation techniques that we have previously used successfully on high profile automotive research and development projects. For the demonstrator plant, we used a different type of control system hardware to what we would typically apply to a vehicle. For vehicles, we would use an automotive electronic control unit (an ECU), but for the plant, we have used a programmable logic controller (PLC). But critically, we’ve done so using our model-based software development techniques, successfully applying the method to the new systems. In effect, we have added capability to the toolset. Capability and best practice can optimise the system and achieve great results for the plant overall.
The benefit for clients of our application of simulation techniques to the demonstrator plant project
For the plant, in order to develop the chemical and thermodynamic cycle, we selected the most appropriate simulation tools for chemical process, thermal and fluids, and we optimised the design of the plant within the constraints of the site and the overall process, to get to an optimally sized demonstrator. We can use those models and simulation to rescale our system for larger processes and applications. This capability is a tremendous benefit for future clients who may want to purchase one or more plants for their sites. By doing this research ourselves, we have accelerated the delivery of the work that we will do for our clients, in effect, we can leverage our learning for their benefit. In this sense, we are not a traditional plant equipment or hardware supplier: we can deliver true consultancy and transfer knowledge to create entirely bespoke designs tailored to the precise requirements and applications of individual clients.
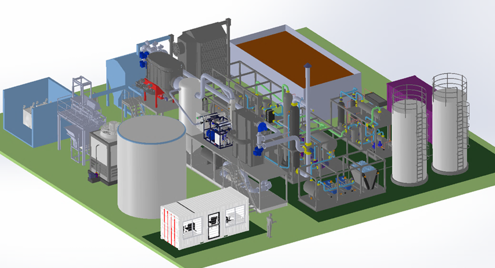
The benefit of applying models in control software development
For the demonstrator plant, we used model-in-the-loop approach in our software development cycles to ‘co-develop’ the design, constantly running it against the system model to confirm correct function. We have used this approach for many years in the automotive sector: taking a model of an engine, motor or after-treatment system. We can start by sketching out a first bit of strategy, then clarify requirements independently, identify what detailed controls we need to operate, and use dynamic simulation to uncover any emergent behaviours we may need to manage. This leads to the development of higher quality control, more rapidly.
The same can be said of the work that our analysis team does on the simulation to optimise the attributes of sub-systems and components, to make sure that the overall system meets a client’s requirements in the most optimal way – whether that is the weight/mass of the plant, or energy usage and so on.
This all ensures genuine scalability and a near granular level of optimisation of the plant – whether in relation to heat exchange or energy levels, or the whole system.
Ricardo benefit: successfully applying multi-industry, multi-domain,
technology-independent thinking
For me, the work we have done on this project very much epitomises what Ricardo does best: working independently across multiple technology portfolios, industry sectors and domains, identifying and analysing the best approaches from each and applying them in a safe, optimised way for our clients so they are getting the best solution for them and their particular circumstances and needs. By having in-depth, expert knowledge of technologies from other industries which could have useful application, we are helping our clients to get to their desired outcome with less risk, more quickly, more safely, and at reduced cost which is essential as they seek to decarbonise their products and operations as part of on-going journeys to net zero.
Find out more about our demonstrator plant
Could your organisation benefit from our capability in energy transition? Get in touch: info@ricardo.com