Rail asset testing and measurement
Integrated rail testing capabilities delivered by local project teams.
Our rail asset Test and Measurements team provide specialist assurance services that enables manufacturers to bring new products to market, as well as investigative and virtual testing capabilities to help asset owners monitor day-to-day performance and rectify issues.
With technical specialists across rolling stock, track, signalling, sub-systems (such as brake systems, pantograph units and catenary) and electro-magnetic compatibility, the expertise we provide is drawn from many years’ experience of rail operations and the surrounding regulatory environment.
As part of Ricardo Certification, our teams operate as a separate and independent business within the Ricardo group and are accredited and appointed to provide assurance and test services by the relevant regulatory authorities.
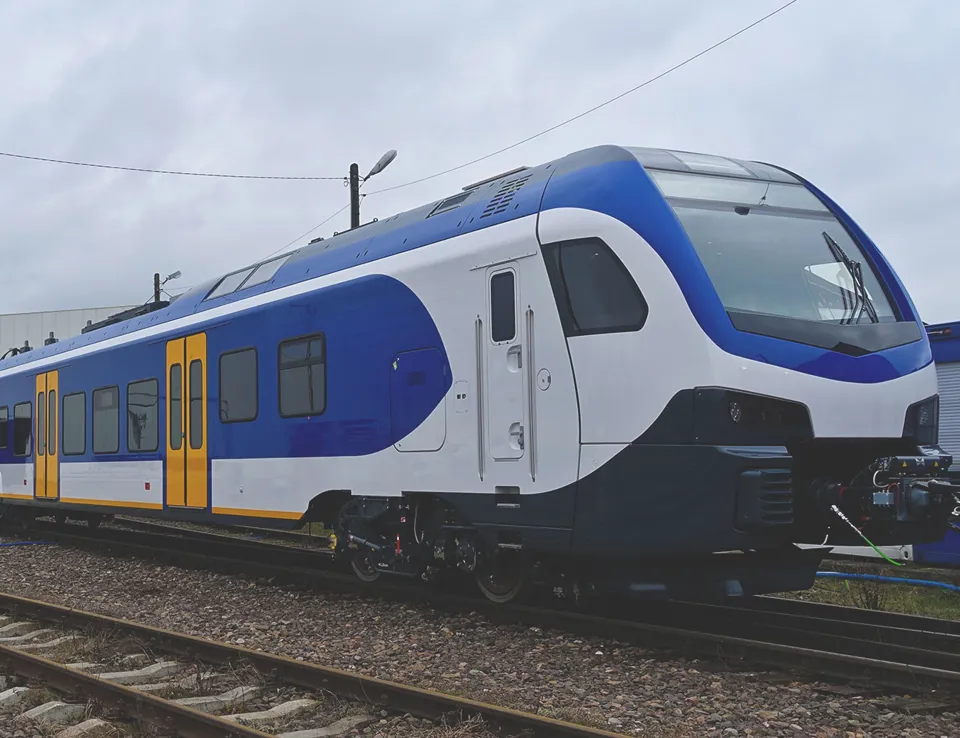
Projects
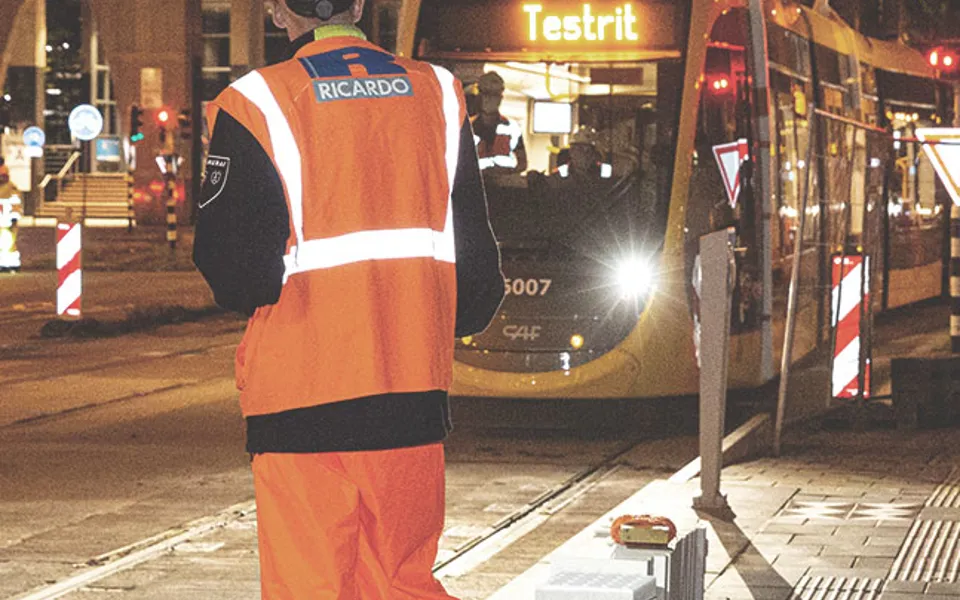
Utrecht tram integration testing
Read case study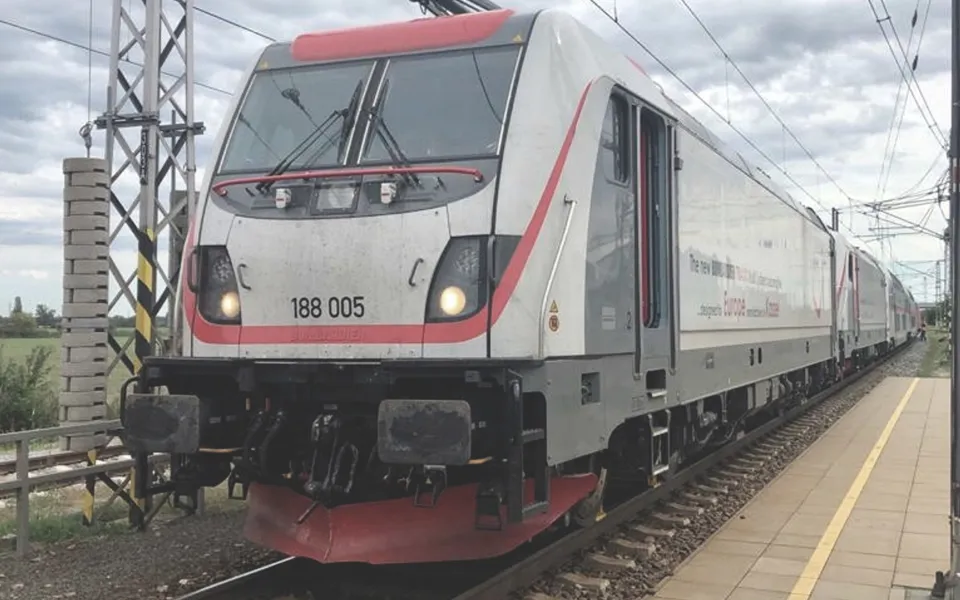
Alstom TRAXX Vehicle Testing
Read case study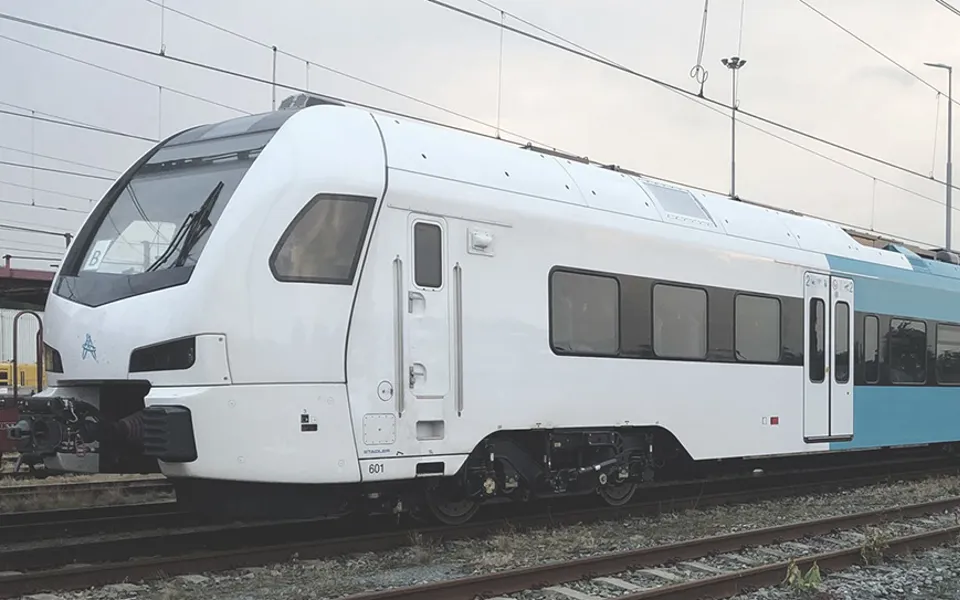
Stadler Wink Authorisation Testing
Read case studyRailway assurance testing
Test programmes to demonstrate compliance with TSIs, UIC and EN standards, as well as national regulations.
Our main capabilities for type testing for authorisation purposes are listed below. All these tests can be performed on a test ring, local tracks or a combination of test locations.
Electrical system compatibility with track circuits and power supply systems
These tests need to be performed in accordance to TSI Loc&Pas, TSI Energy, EN50388, TS50238-2 and NNTR's. Ricardo can perform the required tests and measurements for the following aspects:
DC systems (main focus on The Netherlands and Belgium)
- Compatibility with power supply
- Compatibility with track circuits
AC systems
- Operation within range of voltages and frequencies
- Regenerative brake with energy to the overhead contact line
- Maximum power and current from the overhead contact line
- Power factor
Radiated emissions
For AC and DC systems: field measurement for electromagnetic compatibility according to EN50121-3-1
Axle counter compatibility (EN50592)
For AC and DC systems:
- H-field measurements according to EN50592
- Measurement of the axle counter output
Human exposure (EN50500)
For AC and DC systems: magnetic field measurement according to EN50500.
For pantographs and new catenary systems, which must be tested in accordance with local standards and TSI Loc & Pas, we can offer the following tests and simulations:
- Temperature measurement of the contact area between the catenary wire and contact strips of the pantograph's collector head during standstill current collection (EN50119 and E50367)
- Simulation of the dynamic forces exerted by the pantograph with a model validated for the specific OHL infrastructure (EN50318) (for more information see RiPAC)
- Contact force measurements (EN50317)
- Uplift measurements (EN50317)
Brake performance and wheel slide protection (WSP) system tests have to be performed in accordance with UIC541-05, UIC544-1 and TSI Loc&Pas. We offer the following test services:
Brake performance
Brake performance in accordance with UIC 544-1 and TSI Loc&Pas (referring to EN14531-1)
- Static tests of the braking force and brake pressures
- Dynamic testing on dry track in empty and loaded conditions at different speeds (including maximum brake position)
Wheel slide protection
WSP test in accordance with UIC541-05 and TSI Loc&Pas (referring to EN15595)
- Dynamic testing on track with low adhesion (using soap) for WSP testing at one loading condition
- Very low adhesion test
- Drag Braking test
If required, we can also help to tune the WSP system before commencing official type tests.
The dynamic tests can either be performed on a test ring or on operational tracks. We perform the tests using our measurement platform which has been specifically developed for testing in the rail environment.
To perform the WSP performance tests in a conditioned manner we install soap tanks to supply soap to the wheel / rail contact.
Dynamic behaviour and running-gear measurements have to be performed in accordance with TSI Loc&Pas and EN14363. The tests described in EN14363 are related to derailment / safety and running behaviour.
Depending on the characteristics of the vehicle, it may be necessary to measure the following aspects:
- Forces (wheel/rail and H-forces)
- Accelerations (car body and bogie)
If it is only required to measure accelerations, we will perform these tests using a measurement platform that we have specifically developed for testing in the rail environment. If forces also need to be measured, we work closely with another test institute to instrument the wheelsets.
Furthermore, we can help you with:
- Passenger comfort measurements according to EN12299
- Autonomous monitoring of dynamic performance, for instance in case results of official type tests are not yet available
- Simulations according to Annex T of EN14363 (see multi-body simulations in Rail System Virtual Testing)
Ricardo has years of experience in testing various types of train protection systems, ranging from ETCS to national systems and CBTC.
ETCS/ERTMS
We perform ETCS vehicle/track integration tests according to the ETCS System Compatibility (ESC) requirements, as described in Annex 5 of the Guide for the application of the CCS TSI. Our current experience is mainly in The Netherlands (RLN00445).
Automatic train protection
We can perform static and dynamic calibration of ATB-EG, ATB-NG and STM-ATB in The Netherlands. Furthermore, we can log and analyse the signals from the ATB coils. We use our experience with the various ATB systems also to perform tests with similar systems, like CAWS used in Ireland.
Train detection
Our testing team has in-depth knowledge of the ProRail measurement location used to determine the train detection characteristics and we support the vehicle manufacturers in the execution of test runs at this measurement location.
There are two types of noise measurements that are typically performed as part of vehicle type testing for authorisation:
- Measurements related to TSI Noise
- Measurements related to TSI PRM
TSI Noise
For TSI Noise Ricardo can support with the following measurements related to pass-by and stationary noise:
- Exterior noise at standstill (ISO3095)
- Exterior noise at constant speed (ISO3095)
- Exterior noise when starting the trainset (ISO3095)
- Interior noise measurements in the driver’s cab – driving condition (EN15892)
- Interior noise measurements in the driver’s cab – signal horn in operation (EN15892)
TSI PRM
Related to TSI PRM , Ricardo can support with measurements of the speech eligibility of the PA system (STI/STIPA) and the sound pressure level of the door warning system.
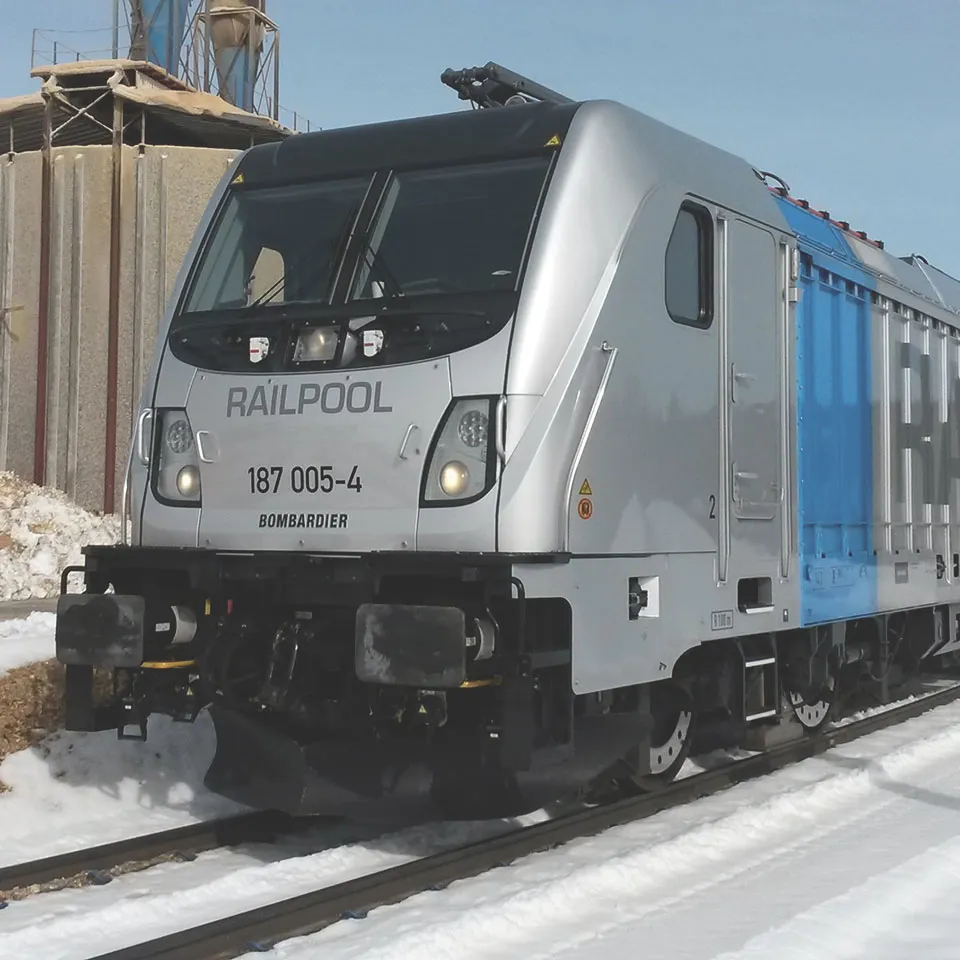
Investigative testing
We offer investigative monitoring and measurement services to help operators, infrastructure managers and vehicle owners monitor asset performance and explore the root cause of sudden degradations.
Conducted on-site or remotely - using state-of-the-art technologies ranging from affordable (IoT) sensor networks to semi-permanent data loggers - each programme is bespoke for your specific purpose, ensuring only the most relevant intelligence is provided to an agreed format and frequency, with minimum disruption to daily operations.
From analysing the findings our experts will advise on options for addressing problems or for optimising processes such as current maintenance regimes, safety management reporting, energy efficiency programmes or noise/vibration reduction.
We also offer a range of on-board and trackside monitoring systems, including a suite of railway digital monitoring services.
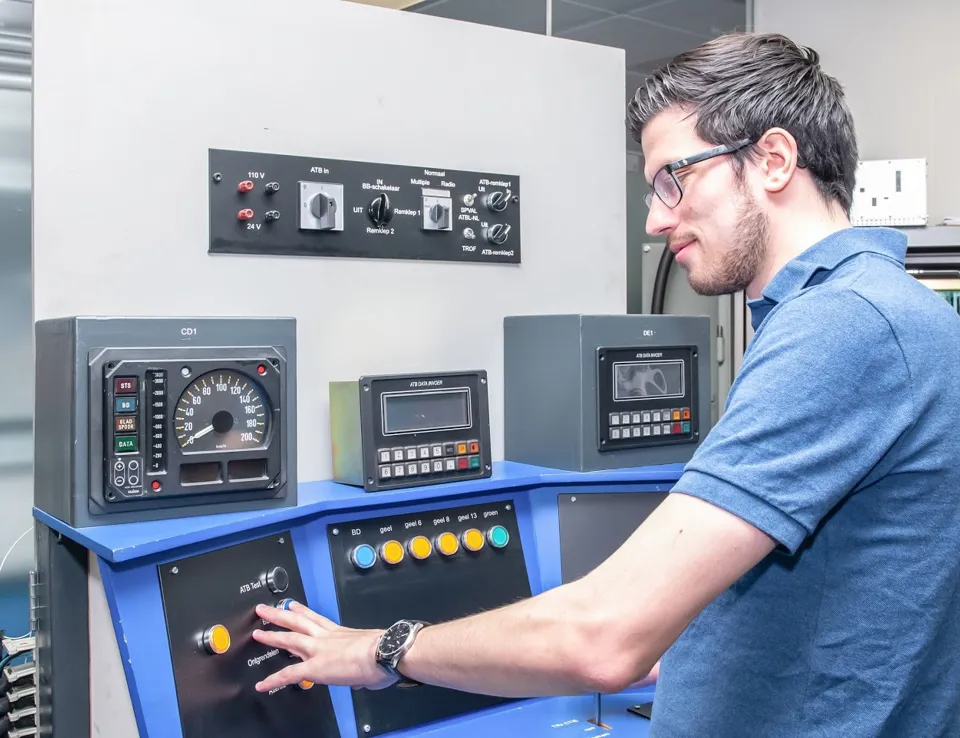
Virtual testing services
Fire safety is an important topic across the rail industry. Whether with regard to rolling stock, or tunnels and stations, it is important to investigate and test evacuation plans.
Similarly, local governments and safety authorities increasingly question the safety of public spaces in the event of fire and require validation of (building) laws.
We can support the decision-making process by providing insight into the development of fire and smoke in the event of a fire. Smoke is particularly important to understand for the correct application of mitigation measures and to evaluate whether built environments adhere to current standards and laws.
We can also provide modelling of passenger flows during evacuation events, which are essential for developing proper measures and escape routes.
Simulations can be used to perform studies of the traction energy supply. Especially when simulating a larger part of the infrastructure, building a model of this infrastructure can be very time consuming.
To overcome this problem, Ricardo developed a method to quickly and automatically build models using information from predefined tables.
We successfully used this method to calculate the average power that can be fed back to the overhead line when the train is recuperating brake energy.
This type of modelling is becoming more interesting, because modern rail vehicles can recuperate brake energy into the overhead line. In DC traction power systems, the power that can be recuperated is limited by other consumers in the vicinity because the energy cannot be fed into the public electricity grid. The power is also dependant on the overhead line voltage. This power is used to calculate the global energy consumption taking into account the recuperation of the rolling stock.
The method is used in our software tool KARPER.*
KARPER calculates the average power that can be recuperated to the overhead line and uses an infrastructure description based on information in tables. These tables contain information about substations, switching stations, stations and track connections. One parameter of the substations model is the average power consumption. In our model, this power consumption is derived from the actual information of the energy meters that are installed in the substations.
Our specialists can quickly configure the input for KARPER and perform recuperation analysis for you. It is also possible to perform other simulations and other analysis with similar simulation models.
With KARPER and our method we can help you with the following types of challenges:
- Determine the recuperation potential by simulation of the infrastructure with recuperating trains on the network
- Performing simulations for delivered power by the substations
- Performing studies on energy losses in the infrastructure
- Performing studies on energy storage
- Performing studies on voltage levels on the pantograph
* KARPER is Dutch for CaRP, the abbreviation of Calculation of Recuperation Potential
For a safe, reliable and efficient operation, the dynamic interaction between vehicle and track plays an important role.
A suboptimal wheel-rail contact will have an adverse effect on running stability, wear and tear, noise, crack initiation in wheel or rail, traction/braking performances, etc.
Investigations into these complex aspects in many cases require the use of advanced Multi-Body System (MBS) modelling techniques.
Within a multi-body virtual environment it is possible to simulate and visualise the dynamic behaviour of the complete vehicle in order to analyse the forces and movements between wheel and rail, between vehicle and track, and between the various subsystems in the vehicle.
Ricardo has been working with advanced multi-body simulation software for more than 20 years, accumulating extensive experience with modelling and analysing the dynamics of complex rail systems.
We use the multi-body simulation package Simpack for vehicle dynamics analyses, the same package used by railway companies and research institutes worldwide.
Each multi-body model we develop is thoroughly validated with measurement data before using it. For certification purposes, we have developed models validated according to EN14363:2016 criteria. We often use Matlab for post-processing of the data produced by our Simpack models.
We apply our experience and knowledge of Multi-Body Simulations for a wide range of services for our clients, for example:
- Assessment of dynamic behaviour according to EN14363:2016 as part of certification, for revision, construction changes or new vehicle subtypes.
- Safety against derailment calculations
Running comfort assessment according to EN12299:2009 - Optimisation of wheel profiles for improvement of wheelset life and ride stability
- Rail profile optimisation for reduction of track forces, wear and noise
- Wheel-rail contact analysis (equivalent conicity, radial steering index, contact stresses, T gamma and RCF damage factors)
- Track friendliness assessments
- Side wind analyses (in combination with CFD simulations)
- Running through switches and crossings related to derailment safety and wear.
- Assessment of track geometry (cant, height, lateral shift) with simplified models based on our Simpack models
To ensure that new pantograph and catenary systems perform according to the European rail industry’s requirements, they must meet the standards set out in the TSI’s.
These standards require that the dynamic interaction - the forces and movements between the systems - is rigorously tested. To date, this has required extensive physical test programmes to assess how the products behave in a fully operational environment.
The Ricardo pantograph and catenary modelling and simulation package, ‘RiPAC’, has been developed to offer track and rolling stock engineers the opportunity to simulate the full motion behaviour of their designs.
By undertaking the test virtually, engineers of pantograph and catenary systems can test designs at earlier stages of development and reduce costly physical testing during certification.
The simulations, which are fully compliant with the applicable standard for current collection systems (EN50318), are performed by Ricardo’s in-house pantograph specialists, who process the data to provide a detailed report. The simulations point out the most critical combinations of vehicles (i.e. pantograph distances) that can subsequently be physically tested.
Ricardo has used RiPAC to examine the catenary of a new line serving the Rotterdam port area for compliance with applicable standards, and has also enabled infrastructure managers to simulate the performance of systems on routes across their networks and identify the cause of dynamical problems and test the impact of modifications.
The use of RiPAC is not limited to conventional rail. We can also provide simulations and analysis for tram systems and catenary-powered bus networks.
The structural integrity of rolling stock is a matter of public safety and failure can have catastrophic consequences.
Ricardo has vast experience in the structural analysis of rail vehicles and can provide unique insights across all phases of the vehicle lifecycle, from conceptual design, certification, operational use and modification, through to end-of-life.
We provide the latest software tools to model components such as wheels, bogie frames, axles, car bodies and track to carry out finite element simulations. Mechanical or thermomechanical loads (for example, for brake discs) can also be applied to the models.
Using knowledge of applicable standards, we can specify required design loads or determine representative in-service load collectives by measurements (for example strain gauge measurements) or multi body simulations.
During post-processing, we will analyse calculated material stresses and assess their levels compared to applicable limit stresses from the relevant standards.
Fracture mechanical calculations can also be performed - for example, for crack growth propagation simulation to support a reliable interval setting of non-destructive testing procedures.
We apply our knowledge of finite element simulations for a wide range of services, including:
- Strength calculation of all types of railway structures
- Design assessments against EN13749, EN 12663-1, EN13103-1, EN13979-1, etc
- Fatigue life prediction (according to FKM Richtlinie)
- Fracture mechanics/crack propagation simulation (root cause analysis)
- Design (and modification) of railway structures from components to vehicles
- Fit for use analysis
- NDT inspection intervals based on fatigue and/or fracture mechanical analysis
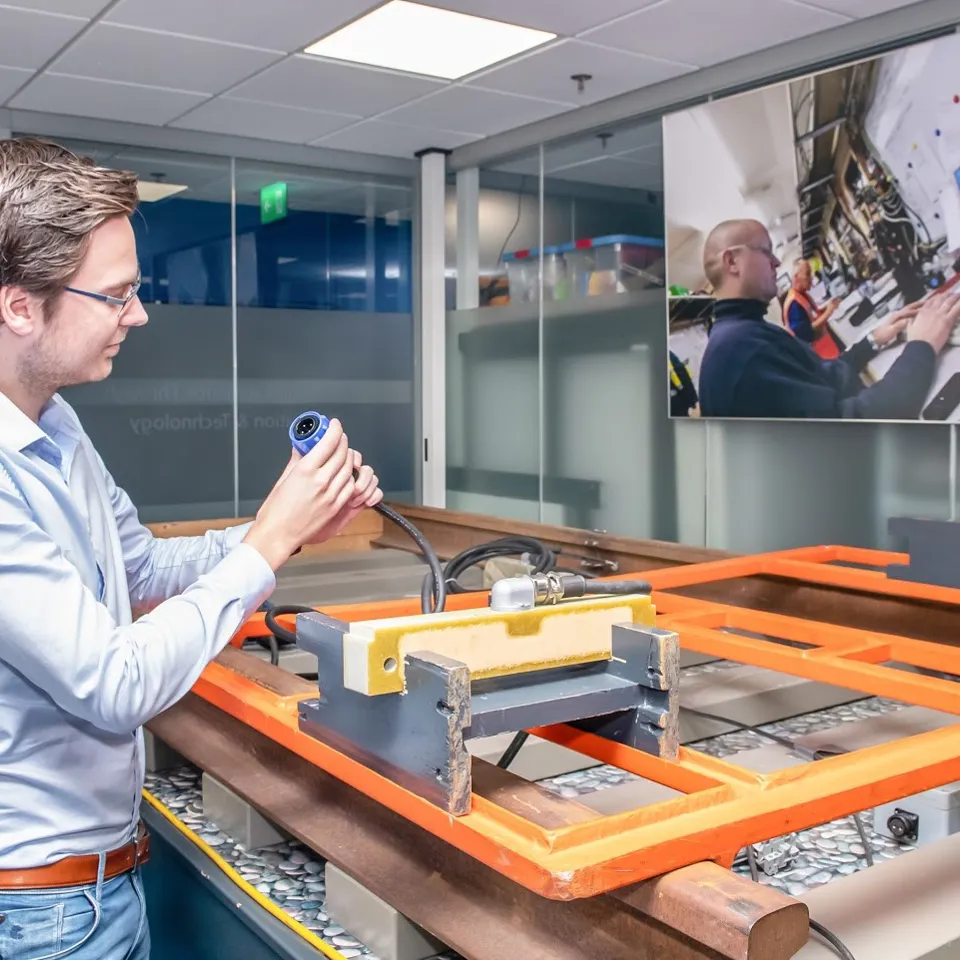
Rail asset testing and measurement Resources